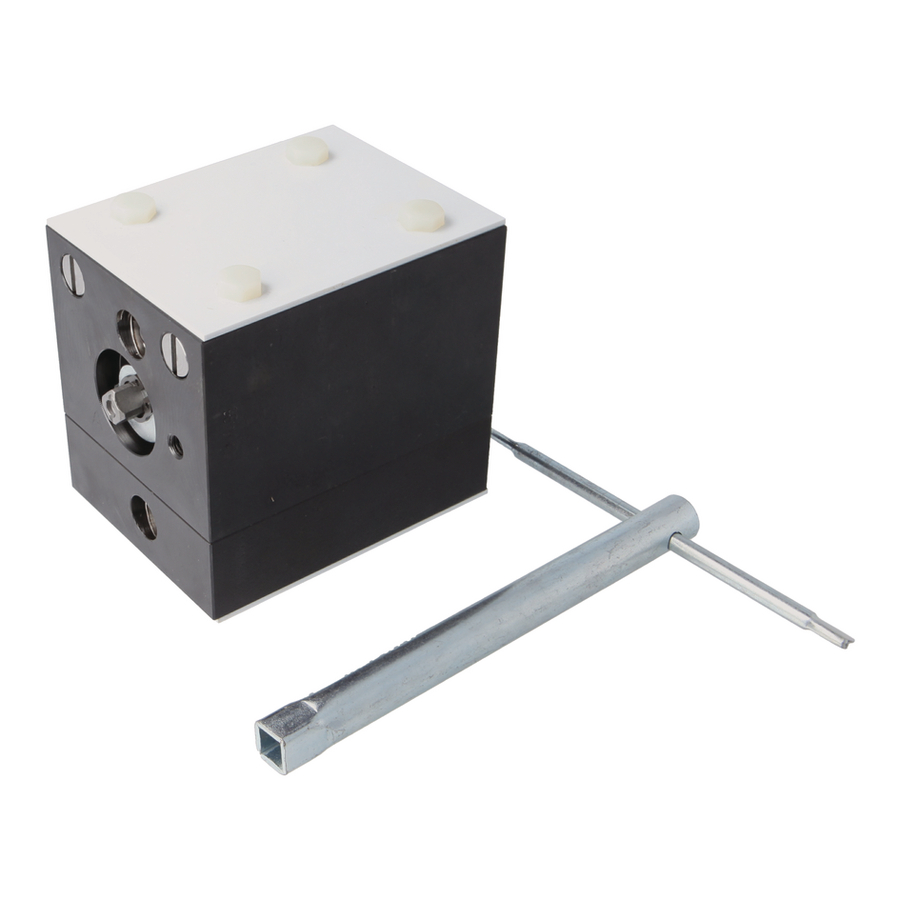
HK GEH ZP NG10 KH
Product information
Description
Because of their high number of control components, large plants are susceptible to malfunctions. If, for example, a solenoid valve fails in the main hydraulic system of a steel rolling mill, this control component must be operated manually or production interrupted until the valve is replaced. To do this, the system must be depressurised, the cylinder, which may be under external pressure, intercepted and the oil drained from the risers to the cylinder. Then, after replacing the solenoid valve, the pipes are refilled and bled.Then, after replacing the solenoid valve, the pipes are refilled and bled.;By the use of this sandwich plate with a ball valve, the directional control valve attached to the plate can be replaced after shutting off all the channels. This is done without depressurising and without draining the system and the associated contamination, without bleeding and without having to take other controls into consideration. This considerably reduces the downtime for hydraulic systems. Starting up the system to bring it into first use is much easier, because it does not have to be drained to replace flushing plates with directional control valves. Furthermore, this can also be done without having to fix any connected cylinders that are under external pressure for the period of servicing. Because the CETOP mounting diagrams on both sides of the connection for the solenoid-operated directional control valves are identical, the sandwich plates can be retrofitted without any problem.
Attributes
- Max. working pressure
- max. 315 bar
- Design
- sandwich body valve
- Connection
- ISO/Cetop 05 size 10